Understanding Reciprocating Pumps: A Comprehensive Guide
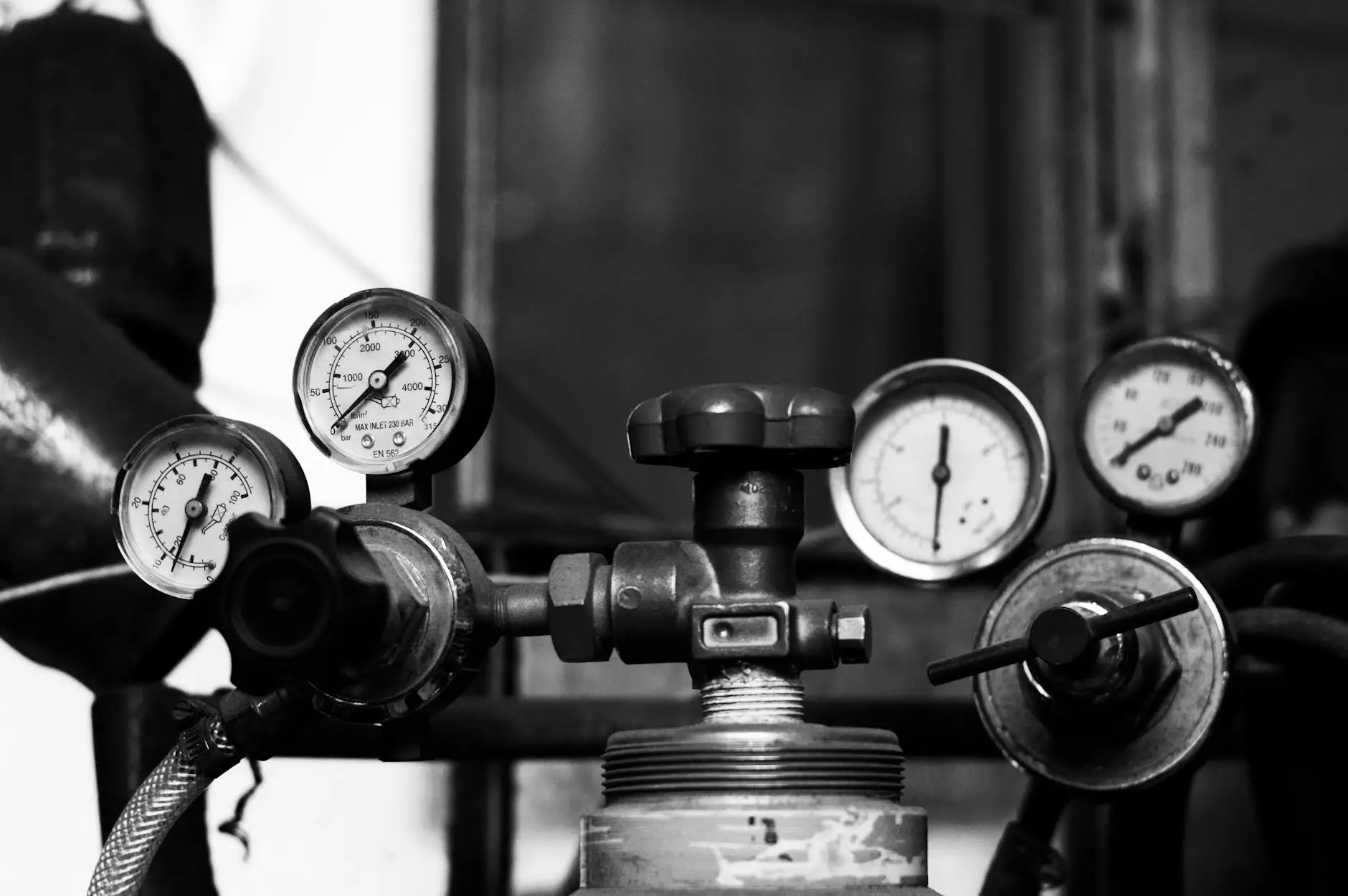
In the realm of fluid mechanics, reciprocating pumps stand out as one of the most essential types of pumps used across various industries. This article delves into the depths of reciprocating pumps, highlighting their construction, functionality, applications, and benefits, especially concerning businesses like Michael Smith Engineers.
What is a Reciprocating Pump?
A reciprocating pump is a type of positive displacement pump that uses a back-and-forth motion to move fluids. This mechanical movement creates a variable volume chamber that fills with fluid on one stroke and discharges it on the next. Reciprocating pumps are highly regarded for their efficiency and ability to handle high-viscosity fluids, making them indispensable in industries ranging from automotive to agriculture.
Types of Reciprocating Pumps
Reciprocating pumps can be classified into several categories, each crucial for specific applications:
- Single-acting pumps: These pumps operate with fluid being displaced in one direction only, making them simple and effective for many tasks.
- Double-acting pumps: These pumps displace fluid during both strokes of the piston, thus generating a continuous flow and increasing efficiency.
- Diaphragm pumps: Utilizing a flexible diaphragm, these pumps are excellent for moving corrosive or viscous fluids without contamination.
- Piston pumps: These are the most common type of reciprocating pumps, using a piston to displace fluid through a cylinder.
How Do Reciprocating Pumps Work?
Understanding the operation of reciprocating pumps is crucial for their effective application in various sectors:
- Intake Stroke: As the piston moves back, it creates a vacuum that draws fluid into the cylinder through an inlet valve.
- Compression and Discharge Stroke: The piston then moves forward, compressing the fluid and forcing it out through an outlet valve.
- Valves Operation: The one-way inlet and outlet valves ensure that fluid flows in the correct direction and prevent backflow.
Applications of Reciprocating Pumps
Reciprocating pumps have a wide array of applications, making them vital in industries such as:
1. Auto Repair
In the automotive sector, reciprocating pumps are essential for various applications, including:
- Fuel Injection Systems: They provide precise fuel delivery to engines, enhancing performance and efficiency.
- Hydraulic Systems: Used in lifting and moving components within vehicles, ensuring smooth functioning of brakes and steering.
2. Farm Equipment Repair
In agriculture, these pumps play a crucial role in:
- Irrigation Systems: Providing reliable water supply to crops, ensuring optimal growth and yield.
- Chemical Application: Used to spray fertilizers and pesticides accurately, minimizing waste and maximizing effectiveness.
3. Structural Engineering
In structural engineering, reciprocating pumps are utilized for tasks such as:
- Concrete Mixing: Ensuring the accurate delivery of concrete mixes to construction sites.
- Water Pressure Systems: Supporting the distribution of water in large civil engineering projects.
Advantages of Reciprocating Pumps
Utilizing reciprocating pumps provides several advantages, including:
- High Efficiency: They can maintain a consistent flow rate and pressure, making them ideal for precision applications.
- Versatility: Able to handle a wide range of fluids, including corrosive and viscous substances.
- Durability: Built to last, often requiring less maintenance compared to centrifugal pumps.
- Cost-Effectiveness: Despite higher initial costs, their efficiency and durability lead to savings over time.
Maintenance of Reciprocating Pumps
To ensure longevity and optimal performance of reciprocating pumps, regular maintenance is crucial. Key maintenance practices include:
- Regular Inspection: Checking for wear and tear on parts, including pistons and valves.
- Lubrication: Keeping moving parts properly lubricated to prevent friction-related damage.
- Cleaning: Regular cleaning of inlet and outlet valves to prevent clogging and ensure smooth operation.
- Fluid Testing: Testing the fluids being pumped to ensure compatibility and performance standards.
Challenges and Considerations
While reciprocating pumps are highly effective, several challenges must be considered when integrating them into a system:
- Pulsation: The fundamental nature of reciprocating pumps leads to pulsating flow, which may necessitate additional dampening equipment.
- Wear and Tear: Critical components may require frequent replacement due to heavy use.
- Space Requirements: They generally require more physical space compared to other types of pumps, such as centrifugal pumps.
Conclusion
In conclusion, reciprocating pumps are indispensable tools across various industries, including auto repair, farm equipment repair, and structural engineering. Understanding their functionality, applications, and maintenance is essential for optimizing their use within your operations. Businesses like Michael Smith Engineers can leverage these insights to improve productivity and efficiency, ensuring that their systems are robust and reliable.
FAQs About Reciprocating Pumps
What is the main difference between reciprocating pumps and centrifugal pumps?
The primary difference lies in their operating principles; while reciprocating pumps use mechanical motion to create pressure and move fluid, centrifugal pumps rely on rotational energy to achieve the same outcome.
How often should reciprocating pumps be serviced?
It is advisable to check reciprocating pumps regularly, with thorough inspections and servicing about every six months or based on the manufacturer's recommendations.
What types of fluids can reciprocating pumps handle?
Reciprocating pumps can efficiently move various fluids, including clean water, oils, chemicals, and slurries, making them versatile for multiple applications.
Can reciprocating pumps be used for high-pressure applications?
Yes, reciprocating pumps are well-suited for high-pressure applications due to their capability to maintain efficiency under substantial pressure.