The Ultimate Guide to **Precision Injection Molding**
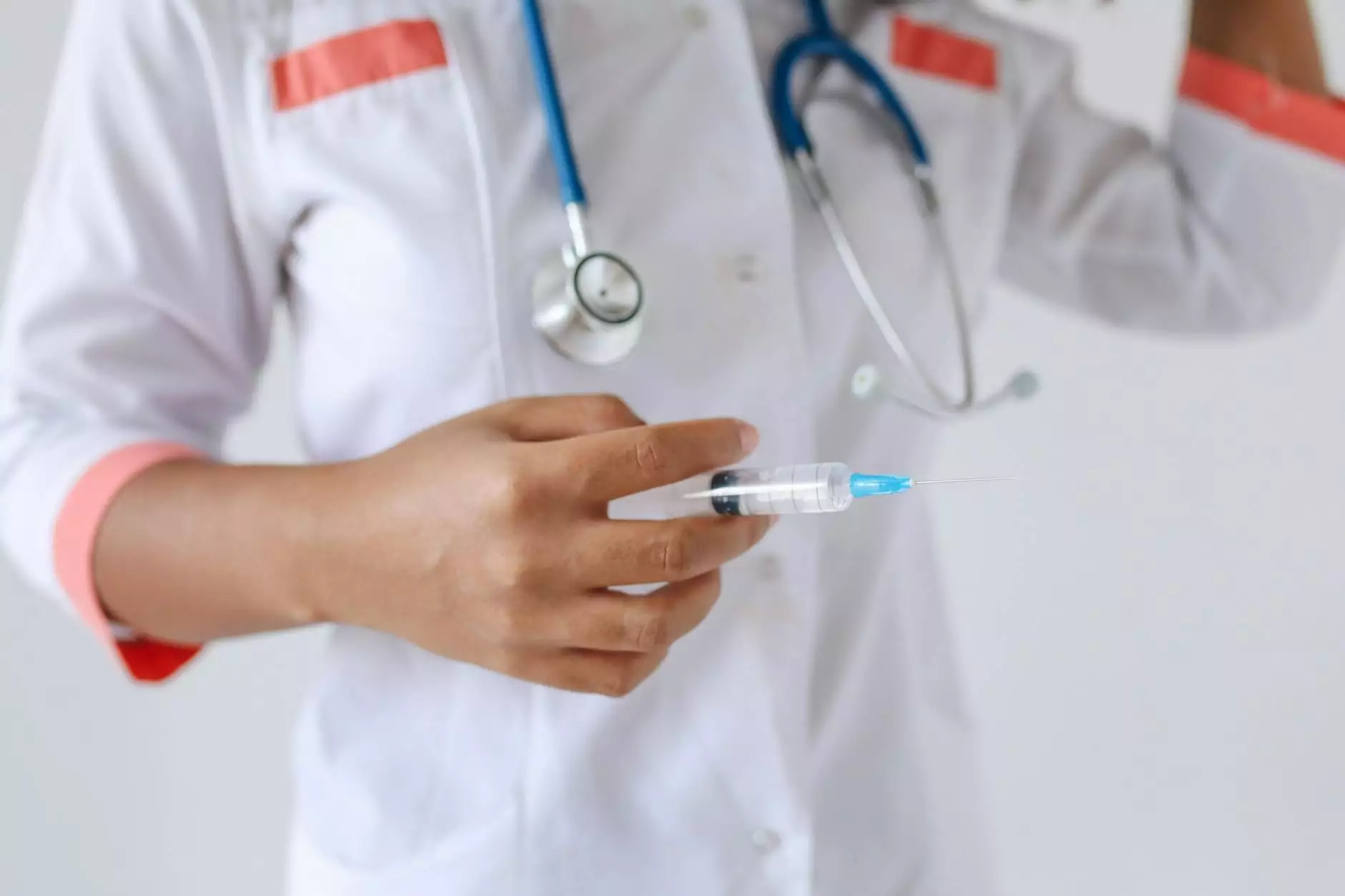
In the rapidly evolving world of manufacturing, the term precision injection mold has become synonymous with innovation, efficiency, and quality. This advanced manufacturing technique is pivotal in various industries, ranging from automotive to consumer goods, where accuracy and detail are paramount. This comprehensive guide will delve deep into the world of precision injection molding, exploring its advantages, processes, and applications.
What is Precision Injection Molding?
Precision injection molding is a manufacturing process used to produce parts with high precision and intricate shapes from thermoplastic materials. The process involves injecting molten plastic into a precisely designed mold, which allows manufacturers to create complex components rapidly and with minimal waste.
Understanding the Process
The process of precision injection molding can be broken down into several key steps:
- Material Selection: Choosing the right thermoplastic material is crucial. Materials can vary in strength, flexibility, and thermal stability, affecting the final product's performance.
- Mold Design: Designing the mold involves creating a blueprints that dictates the shape and dimensions of the final product. CAD software is often used for accuracy.
- Melting the Material: The selected thermoplastic material is heated until it reaches a molten state for injection.
- Injection: The molten material is injected under high pressure into the mold cavity, ensuring that it fills every detail of the mold.
- Cooling: Once filled, the mold is cooled, hardening the material into the desired shape.
- Demolding: After cooling, the mold is opened, and the final product is ejected, ready for finishing processes.
Key Benefits of Using Precision Injection Molding
The adoption of precision injection molding in manufacturing processes offers numerous advantages:
1. High Accuracy and Precision
One of the most significant benefits of precision injection molding is its ability to produce highly intricate parts with exceptional accuracy. This level of precision is essential in industries like automotive and aerospace, where even the slightest deviation can lead to catastrophic failures.
2. Cost-Effectiveness
While the initial setup costs, including mold design and fabrication, may be high, the long-term savings are substantial. Precision injection molding minimizes waste, reduces material costs, and allows for mass production, making it a cost-effective solution in the long run.
3. Versatility in Design
The flexibility of the molding process allows for the creation of a wide variety of products ranging from simple components to complex structures. Innovators can experiment with designs without extensive re-engineering efforts.
4. Enhanced Material Properties
Precision injection molding techniques often result in enhanced material characteristics such as improved strength and durability. The controlled cooling processes can also lead to superior surface finishes, which can reduce or eliminate the need for subsequent finishing or machining.
5. Scalability
This process is highly scalable. Once the mold is created, companies can produce thousands or even millions of identical parts. This feature is particularly beneficial for businesses experiencing increased demand for their products.
Applications of Precision Injection Molding
With its versatility, precision injection molding is employed across various sectors, including:
- Automotive Industry: Creating components such as dashboard parts, connectors, and housings.
- Medical Devices: Manufacturing high-precision parts for medical equipment, including surgical devices and housings for diagnostics equipment.
- Consumer Products: Producing items like packaging, toys, and household appliances that require intricate designs.
- Electronics: Designing and fabricating components such as connectors and casings for electronic devices, ensuring safety and reliability.
- Aerospace: Producing lightweight and strong components that meet stringent industry standards for safety.
Challenges in Precision Injection Molding
While precision injection molding presents numerous advantages, it is not without its challenges:
1. Initial Setup Costs
The design and fabrication of molds can be expensive and time-consuming. Companies must weigh these upfront costs against the expected production volume and demand.
2. Technical Expertise Required
The complexity of the process requires skilled technicians and engineers to ensure the molds are produced accurately and efficiently. A lack of expertise can lead to production errors and increased costs.
3. Material Limitations
Not all materials are suitable for precision injection molding. Manufacturers must choose appropriate thermoplastics that meet the requirements of their specific application, which can limit design choices.
Future Trends in Precision Injection Molding
The landscape of precision injection molding is ever-evolving, driven by technological advancements and market demands. Here are some future trends to watch:
1. Automation and Robotics
Incorporating automation and robotics into the injection molding process can significantly enhance efficiency and reduce labor costs. Automated systems can manage material loading, part ejection, and even assembly operations.
2. Sustainable Practices
As environmental concerns grow, manufacturers are seeking sustainable materials and processes. Innovations in biodegradable plastics and recycling methods will likely shape the future of precision injection molding.
3. Digital Integration
The integration of digital technologies like IoT (Internet of Things) and AI (Artificial Intelligence) for predictive maintenance, quality control, and process optimization will streamline operations and enhance product quality.
How to Choose the Right Partner for Precision Injection Molding
Selecting the right partner for your precision injection molding needs is crucial for success. Consider the following factors:
1. Experience and Expertise
Look for companies with a proven track record in your specific industry. Experienced partners will understand the unique challenges you face and provide tailored solutions.
2. Technological Capabilities
Ensure that your partner utilizes advanced technologies and equipment. This can significantly impact the precision and quality of the molds they produce.
3. Quality Control Processes
A robust quality control process is essential for maintaining product standards. Inquire about their testing methods and certifications.
4. Communication and Support
Effective communication is vital for a smooth partnership. Choose a provider that prioritizes customer service and is flexible in addressing your needs.
Conclusion: Embracing Precision Injection Molding for Business Success
In conclusion, precision injection molding is an indispensable process in modern manufacturing. Its ability to produce high-quality, precise parts quickly and cost-effectively makes it a preferred choice across various industries.
As technology continues to advance, the future of precision injection molding looks promising, with innovations aimed at improving efficiency, sustainability, and design capabilities. By understanding the intricacies of this process and collaborating with the right partners, businesses can harness its potential to achieve unmatched success in their respective markets.